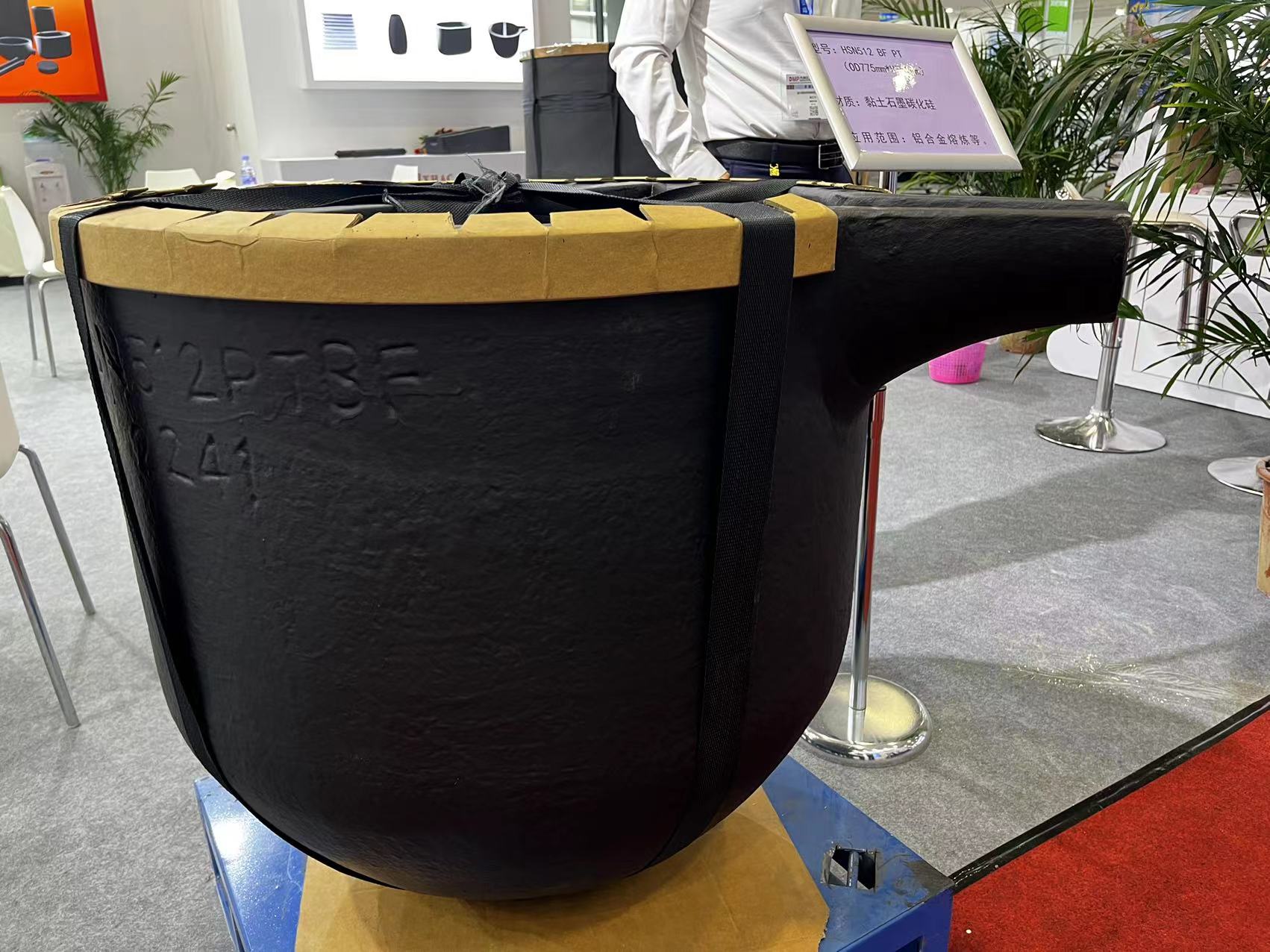
Forberedelsesmetoden for høy styrkegrafitt silisiumkarbid digelFor metallsmelting inkluderer følgende trinn: 1) råstoffforberedelse; 2) primær blanding; 3) Materiell tørking; 4) knusing og screening; 5) sekundær materialforberedelse; 6) sekundær blanding; 7) pressing og støping; 8) skjæring og trimming; 9) tørking; 10) glass; 11) primær skyting; 12) impregnering; 13) sekundær skyting; 14) belegg; 15) Ferdig produkt. Digelen produsert ved hjelp av denne nye formelen og produksjonsprosessen har sterk høye temperaturmotstand og korrosjonsmotstand. Den gjennomsnittlige levetiden til digelen når 7-8 måneder, med en enhetlig og defektfri indre struktur, høy styrke, tynne vegger og god termisk ledningsevne. I tillegg forbedrer glasurlaget og belegget på overflaten, sammen med flere tørking og skyteprosesser, produktets korrosjonsbestandighet betydelig og reduserer energiforbruket med omtrent 30%, med en høy grad av forglassing.
Denne metoden involverer feltet ikke-jernholdig metallurgi-støping, spesielt preparatmetoden for høy styrke grafitt silisiumkarbid-digel for metallsmelting.
[Bakgrunnsteknologi] Spesielle grafitt-silisiumkarbid-digler brukes hovedsakelig i ikke-jernholdige metallstøping og smiingsprosesser, samt i utvinning og raffinering av edle metaller, og produksjon av høye temperaturer og korrosjonsresterende produkter som kreves for plast, keramikk, glass-sement.
Eksisterende spesielle grafitt -silisiumkarbidgruppeformuleringer og produksjonsprosesser produserer produkter med en gjennomsnittlig levetid på 55 dager, noe som er for kort. Bruk og produksjonskostnader fortsetter å øke, og mengden av avfall som genereres er også høy. Derfor er å forske på en ny type spesiell grafitt -silisiumkarbid -digel og produksjonsprosessen et presserende problem å løse, ettersom disse diglene har betydelige anvendelser innen forskjellige industrielle kjemiske felt.
[0004] For å løse de ovennevnte problemene, leveres en metode for å fremstille grafitt silisiumkarbid-digler for metallsmelting. Produkter utarbeidet i henhold til denne metoden er motstandsdyktige mot høye temperaturer og korrosjon, har en lang levetid og oppnår energibesparelser, utslippsreduksjon, miljøvern og høy resirkulering av avfall under produksjonen, og maksimerer sirkulasjonen og utnyttelsen av ressursene.
Forberedelsesmetoden for høystyrke grafitt silisiumkarbid digler for metallsmelting inkluderer følgende trinn:
- Råstoffforberedelse: Silisiumkarbid, grafitt, leire og metallisk silisium er plassert i deres respektive ingredienshoppere med kran, og PLC -programmet kontrollerer automatisk utslipp og veiing av hvert materiale i henhold til det nødvendige forholdet. Pneumatiske ventiler kontrollerer utslippet, og minst to veiesensorer er satt nederst på hver ingrediensbeholder. Etter veiing plasseres materialene i en blandemaskin av en automatisk bevegelig vogn. Den første tilsetningen av silisiumkarbid er 50% av det totale beløpet.
- Sekundærblanding: Etter at råvarene er blandet i mikseverdimaskinen, slippes de ut i en bufferbeholder, og materialene i bufferbeholderen løftes til blandingsbeholderen med en bøtteheis for sekundær blanding. En fjerningsanordning for jern er satt til utløpsporten på bøtteheisen, og en vanntilsetningsanordning er satt over blandingsbeholderen for å tilsette vann mens du omrøres. Vanntilsetningshastigheten er 10L/min.
- Materiale tørking: Det våte materialet etter blanding tørkes i et tørkeutstyr ved en temperatur på 120-150 ° C for å fjerne fuktighet. Etter fullstendig tørking tas materialet ut for naturlig kjøling.
- Knusing og screening: Det tørkede klumpete materialet kommer inn i et knusings- og screeningsutstyr for forhåndsknusing, går deretter inn i en motangrepsknuser for ytterligere knusing, og passerer samtidig gjennom et 60-mesh screeningsutstyr. Partikler som er større enn 0,25 mm returneres for gjenvinning for ytterligere forhåndsknusing, knusing og screening, mens partikler mindre enn 0,25 mm blir sendt til en hopper.
- Sekundær materialforberedelse: Materialene i utladningshopper blir transportert tilbake til batchmaskinen for sekundær preparat. De resterende 50% av silisiumkarbid tilsettes under sekundærforberedelsen. Materialene etter sekundærforberedelsen sendes til mikseverdimaskinen for omblanding.
- Sekundær blanding: Under den sekundære blandingsprosessen tilsettes en spesiell løsning med viskositet til blandingsbeholderen gjennom en spesiell løsning som legger til enhet med en spesifikk tyngdekraft. Den spesielle løsningen veies av en veiingsbøtte og legges til blandingsbeholderen.
- Trykk og støping: Materialene etter sekundærblandingen sendes til en isostatisk pressende maskinbeholder. Etter lasting, komprimering, støvsuging og rengjøring i formen, presses materialene i den isostatiske pressemaskinen.
- Kutting og trimming: Dette inkluderer å kutte høyden og trimme digelen. Kutting gjøres av en skjæremaskin for å kutte digelen til den nødvendige høyden, og burrs etter skjæring er trimmet.
- Tørking: Digelen, etter å ha blitt kuttet og trimmet i trinn (8), sendes til en tørkende ovn for tørking, med en tørketemperatur på 120-150 ° C. Etter tørking holdes det varmt i 1-2 timer. Tørkeovnen er utstyrt med et justeringssystem for luftkanal, som består av flere justerbare aluminiumsplater. Disse justerbare aluminiumsplatene er anordnet på de to indre sidene av tørkeovnen, med en luftkanal mellom hver to aluminiumsplater. Gapet mellom hver to aluminiumsplater justeres for å regulere luftkanalen.
- Vinduer: Glasuren er laget ved å blande glasurmaterialer med vann, inkludert bentonitt, ildfast leire, glasspulver, feltspatpulver og natriumkarboksymetylcellulose. Glasuren påføres manuelt med en børste under glass.
- Primær skyting: Digelen med påført glasur avfyres en gang i en ovn i 28-30 timer. For å forbedre skyteeffektiviteten, settes en labyrint ovnsseng med en tetningseffekt og luftblokkering på bunnen av ovnen. Ovnsengen har et bunnlag med tetningsbomull, og over tetningsbomullet er det et lag med isolasjonsmurstein, og danner en labyrint ovnsseng.
- Impregnering: Den avfyrte digelen er plassert i en impregneringstank for vakuum og trykkimpregnering. Impregneringsløsningen transporteres til impregneringstanken gjennom en forseglet rørledning, og impregneringstiden er 45-60 minutter.
- Sekundærskyting: Den impregnerte digelen plasseres i en ovn for sekundær avfyring i 2 timer.
- Belegg: Digelen etter sekundær avfyring er belagt med en vannbasert akrylharpiksmaling på overflaten.
- Ferdig produkt: Etter at belegget er fullført, er overflaten tørket, og etter tørking er digelen pakket og lagres.
POST TID: MAR-20-2024